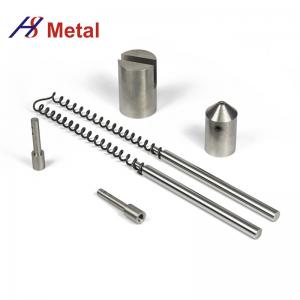
Add to Cart
1,Description:
Tungsten heating vacuum coating offers several advantages. Tungsten has a high melting point and excellent thermal stability, making it suitable for applications requiring high-temperature environments or thermal shock resistance. Additionally, tungsten exhibits good adhesion to various substrates, ensuring a strong bond between the deposited film and the substrate surface.
The properties of the deposited tungsten film can be controlled by adjusting the process parameters, such as the evaporation temperature, deposition rate, and deposition time. This allows for the customization of film thickness, surface roughness, and other desired characteristics.
Tungsten heating vacuum coating finds applications in various industries. It is commonly used in the production of electrical and electronic devices, such as thin-film transistors (TFTs), integrated circuits (ICs), and display technologies like flat-panel displays and touchscreens. Tungsten coatings are also employed in optical coatings, corrosion protection, and wear-resistant applications.
The resulting tungsten coating exhibits high electrical conductivity, excellent thermal conductivity, and good corrosion resistance. These properties make tungsten heating vacuum coating a valuable technique for enhancing the performance and durability of components in diverse industries.
2,Specifications:
Physical Property | Value |
---|---|
Density | 19.3 g/cm³ (tungsten) |
Melting Point | 3,422°C (tungsten) |
Thermal Conductivity | 173 W/m·K (tungsten) |
Coefficient of Thermal Expansion | 4.5 x 10^-6 /°C (tungsten) |
Electrical Conductivity | 31% IACS (International Annealed Copper Standard) (tungsten) |
Hardness (Vickers) | 343 HV (tungsten) |
Film Thickness | Variable, typically in the range of a few nanometers to micrometers |